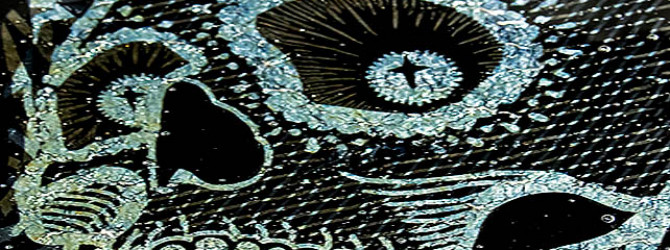
Irid-on-Irid Fusing
Introduction
Iridized glass is one of the most exciting materials available to fused glass artists. Because it is not fully understood by many kilnformers, it is unfortunately not used as widely as it could be.
This tutorial has two goals:
- First, it explains what iridized glass is and how it is made.
- Second, it takes you, step-by-step, through the process of making a finished irid-on-irid project using the same technique used to make this work:
Editor’s Note: Photographing glass is difficult. The transparency and glare often make it difficult to see what’s important. Add an iridized surface to the mix and it can be a photographer’s nightmare. For this tutorial, having pictures that make clear what is going on was considered more important than having pictures that are beautiful. Some colors and shading have been deliberately distorted to make the image more “readable”.
What is Iridized (“Irid”) Glass) ?
Iridized glass is “normal” glass that has a thin, metallic coating on one surface. The most common iridized coating colors for fusible glass are gold, silver, and rainbow. Some manufacturers also apply iridizations with pattern effects. Here’s a picture of the standard iridized colors offered by Bullseye Glass:
To understand how iridized glass is made, take a look at this excellent video from the world’s foremost glass experts, Corning Museum of Glass:
Click above image to launch video in new window.
More than just a pretty surface, iridization changes the way glass behaves. To learn about that, continue reading.
How Iridized Glass Behaves
There are three things you should know about working with iridized glass:
-
- Iridized surfaces do not stick. Just like dichroic glass and micas, the iridized surface on glass never melts and never gets “sticky”. If you try and fuse two pieces of iridized glass together, with the iridized surfaces facing each other, they won’t fuse together. Glass will fuse to iridized glass only when there is “bare” glass in contact with the iridized surface.
- The iridized surface doesn’t stretch. Because the iridized surface doesn’t melt, it cannot stretch. If the glass under the irid spreads, the iridized surface crackles like this:
- Iridized glass reflects heat. Projects with large areas of iridized glass are more prone to thermal-shock since the iridized surface reflects more radiant heat than the non-iridized surface. For this reason, you should always decrease heating and cooling rates for schedule segments below 1000° F (538° C).
The first item above, that iridized surfaces won’t stick to each other, is at the heart of the irid-on-irid technique. Let’s get started!
How the Technique Works
While iridized surfaces won’t stick to each other, they will stick to non-iridized glass. By strategically sandblasting away some of the iridization on two sheets of glass, you can get enough of the glass to fuse so that the places where irids overlap will not be a problem. If that sounds a bit confusing, don’t worry. The next few illustrations will explain.
Step 1: Mask the Iridized Surfaces
The above illustrates two pieces of iridized glass. The top left piece is blue glass with iridization and the bottom left piece is clear glass with iridization. Masking tape stripes are applied to the iridized surface of each piece, as shown on the right.
Step 2: Sandblast the Glass
The iridized film is very thin and can be quickly and easily removed in a sandblaster. Masking tape will protect the iridized surface. When tape is used this way it is called a “resist” because it resists the sandblasting.
We can see this process in the following sequence of pictures:
Here, again, we have the blue glass with iridization on the top and the clear glass with iridization on the bottom.
The first set (on the left) are as we left them in the last image – masked with tape.
In the images in the middle, the exposed iridized surface has been blasted away, leaving only the bare glass (and the iridization that is currently hidden beneath the tape).
In the images on the right, the tape has been removed revealing the iridization that was protected by the tape resist.
Step 3: Stack the Layers
The next step is to properly orient and stack the two layers.
First, flip the clear layer over so that the iridized stripes face down. Now, rotate the clear piece a quarter turn (90°) so that the stripes run the opposite way (horizontally) of those on the blue glass (vertically). Place the clear piece on top of the blue piece and you’ll see something like what’s shown in the tile on the right (above) and enlarged (below).
With the two layers stacked, and with irid surfaces facing each other, there are four possible combinations:
- Where the iridized (unblasted) surface of the blue glass touches the blasted surface of the clear glass.
- Where the iridized (unblasted) surface of the clear glass touches the blasted surface of the blue glass.
- Where the blasted surfaces of both glasses touch each other.
- Where the iridized (unblasted) surfaces of both glasses touch each other.
Only the spaces where irid is touching irid will not fuse together. Every place else fuses just fine! In most cases, that is more than sufficient to create a fused, stable project.
Here’s a photo showing the exercise above in actual glass:
Irid-on-Irid Project Overview
Now you can put your understanding of iridized glass to use in a fused glass project.
To complete this project, you’ll need the following:
Basic fusing tools:
As with most glass fusing projects, you’ll need a glass cutter and a kiln. It is important that you fire this project on a kiln washed (primed) shelf without any shelf paper or fiber paper in the kiln. This is explained in the section on firing the glass.
Iridized glass:
You need two pieces of iridized glass where each is the size of the finished work. In the example shown here we use two 6 x 10 inch (15 x 25 cm) pieces.
The best results are usually achieved using a clear iridized layer and a colored iridized layer. Avoid using glass where the glass color and iridized color are low contrast. For example, amber glass with a gold iridized surface rarely produces satisfying results. Using a clear iridized glass on top of a black iridized glass almost always works well. When making large projects, consider small tests to ensure that you will be happy with the results.
Resists:
Materials used to protect areas of iridized surface during blasting are called “resists.”
While there are heavy-duty vinyls manufactured for this purpose, they are really overkill for this technique. Iridized surfaces are very thin and light sandblasting removes them quickly. For this project, masking tape and white (Elmer’s style) glue are ideal and inexpensive.
Sharp craft knife:
For cutting your design in masking tape, nothing beats a new craft blade. Dull blades will tear the tape, leaving rough edges.
Sandblaster:
Most glass sandblasters use either aluminum oxide or silicon carbide (carborundum) as blasting medium. For this project, you must use aluminum oxide. Silicon carbide fractures glass at a microscopic level and usually results in an unattractive haze when blasted surfaces are sandwiched between layers of glass (as we do here).
With everything we need ready to go, let’s start the project!
Project Step 1: Mask
Designing your project is a critical step for irid-on-irid fusing. Here are two important guidelines:
- Leave about 0.5 inch (12 mm) around the edge of both pieces of glass unmasked. This will ensure that both layers fuse together.
- Design so that you have a good mix of overlapping and non-overlapping irid. The beauty of this technique comes from the different possible irid combinations.
There are different approaches to masking with tape. You may cut designs out of the tape and then apply them to the glass OR you can simply cover areas of glass with wide swaths of tape and, using the craft knife, cut and peel away the area you want to expose.
When using white glue to draw lines, keep in mind that crossed lines will flow together. To maintain crisp intersections of glue lines, draw one line first, allow it to dry, and then draw the crossing line.
Here are the masked pieces of glass for the example shown in this tutorial, using both tape and glue (in this case for dots):
The black circles on the clear glass are marker lines on the back side of the glass. They’ll burn away during the firing.
Notice that the outer margins of both pieces of glass are bare, in accordance with the first design guideline above. This will allow for a glass-to-glass fuse all around the edge of the project.
The glass is ready for the sandblaster!
Project Step 2: Sandblast
Make sure that all glue is dry and that all tape is securely burnished to the glass. If your sandblaster allows you to adjust pressure, turn it down to about 25 PSI.
Place the glass in the cabinet and, keeping the blast nozzle several inches away from the glass, remove the exposed iridized surface. For best results, alternate sweeping sideways and up-and-down for even blasting.
Check the glass to make sure no iridization is visible:
If you see bits of irid remaining, mark them with a magic marker to make finding them in the cabinet easier and re-blast.
Important! Do not over-blast the glass. Carving too deeply into the glass will result in air-trapping texture and undesirable bubbles.
One you are done blasting away the exposed iridized surface, peel off the tape and remove the glue with warm water and a scrub brush. Make sure not to use any brush that might scratch the glass.
Here are the two pieces of glass after blasting and cleaning:
Clean the glass well and it is time to fuse them together!
Project Step 3: Fire!
Stack the glass so that the blasted surfaces are placed against each other:
Align the edges:
Full fuse the glass on a shelf using only shelf primer. Do not use any shelf or fiber paper! Shelf paper and fiber paper create carbon when they burn. That fine ash can become trapped in the ground, sandblasted surface. When that happens, the project takes on an unpleasant gray hazing near the edges.
Here’s the firing schedule, using Fahrenheit:
Segment | Ramp | Target | Hold |
1 | 200° F / hr | 1225° F | 30 minutes |
2 | FULL | 1450° F | 20 minutes |
3 | FULL | 950° F | 45 minutes |
4 | 100° F / hr | 725° F | none |
Here it is using Celsius:
Segment | Ramp | Target | Hold |
1 | 111° C / hr | 663° C | 30 minutes |
2 | FULL | 768° C | 20 minutes |
3 | FULL | 510° C | 45 minutes |
4 | 56° C / hr | 385° C | none |
Project Wrap-Up
Once your project is fused, you can slump it any way you would like!
When slumping iridized projects, keep in mind these two important facts from the beginning of this tutorial:
- An iridized surface on glass doesn’t stretch. If you slump an iridized piece of glass into a deep mold, the irid will likely take on a crackled appearance.
- Iridized glass reflects heat differently from non-iridized glass. This can make iridized projects more likely to thermal-shock. Conservative firing schedules for iridized projects heat and cool more slowly below 1000° F (538°).
Here’s a close-up photo of the finished glass:
And here’s the completed project:
Enjoy!