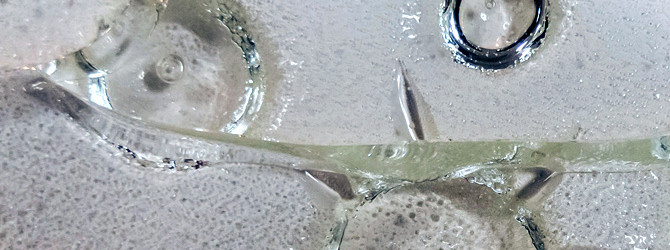
Understand and Avoid Thermal Shock
If you’ve ever had a piece of work break in the kiln then you might have been the victim of thermal shock.
In this tutorial we explain what thermal shock is, what causes it, and – most importantly – how to avoid it.
To navigate this tutorial, click a link in the list below to jump directly to that section OR navigate forward and backwards using the links in the blue bar below.